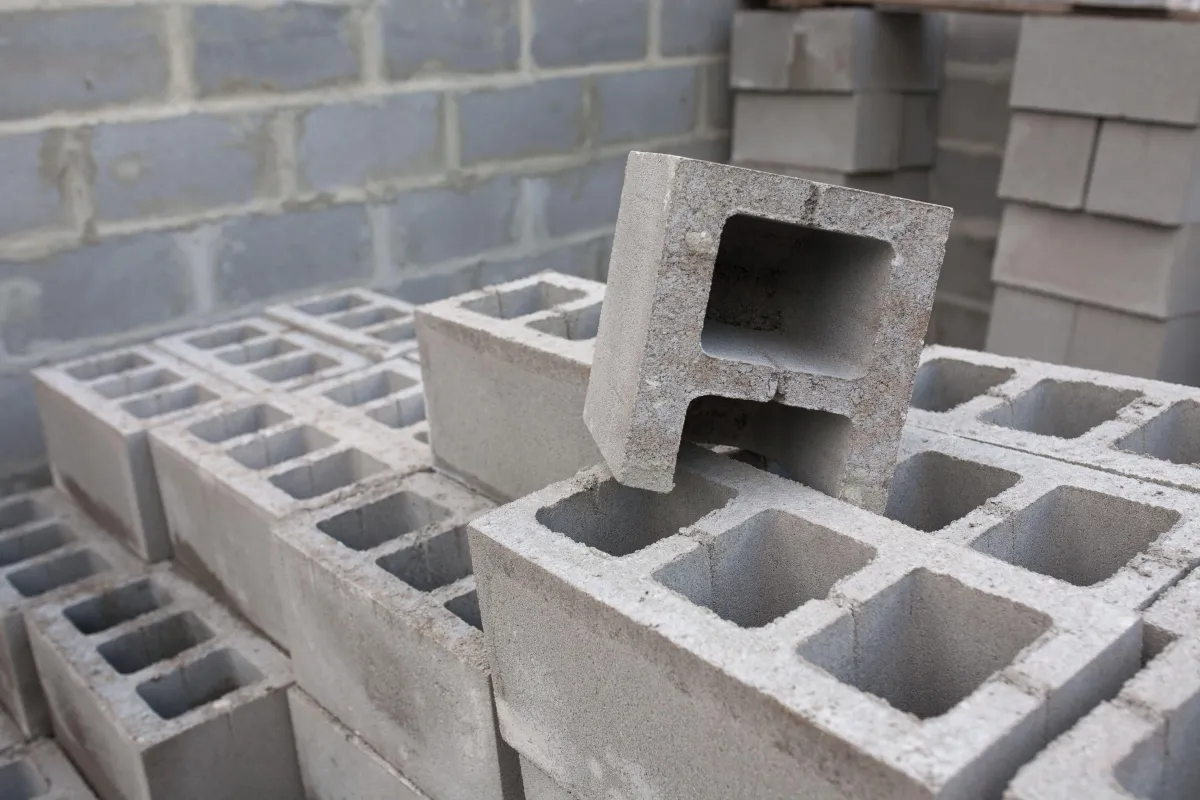
high-quality concrete blocks
🧱 Why high-quality concrete blocks are the key to long-term success in concrete manufacturing
high-quality concrete blocks
🧱 Why high-quality concrete blocks are the key to long-term success in concrete manufacturing
1. 🧪 Quality Mix: The Foundation of Every Reliable Concrete Block
⚙️ Key Elements of a Quality Mix
1.2. Tight Water/Cement Ratio Control
2. 💧 Moisture Sensors: The Technology That Guarantees Batch-to-Batch Consistency
⚙️ Recommended Sensor Types & Applications
🔄 Integration with Automation CBM
3. 🔩 High-Quality Molds: The Unsung Heroes of Precision and Efficiency
⚙️ Mold Construction Standards for Top Performance
🧠 Best Practices for Mold Management
📈 Results of Using High-Quality Molds
4. 🛠️ Calibrated Equipment: Precision That Pays Off in Every Production Cycle
🧠 Why Calibration Is Non-Negotiable
⚙️ What Needs Calibration and How Often
🔧 Best Practices for Calibration & Maintenance
5. 🏅 High-Quality Concrete Blocks: The Result That Impacts Your Business
🧠 What Defines a High-Quality Concrete Block?
💡 Why These Blocks Make the Difference
🔁 How to Ensure This Level of Quality
❓ Frequently Asked Questions About Concrete Block Quality in Vibrocompacted Plants
🔹 What’s more important: the concrete mix or the block machine?
🔹 How often should I calibrate my block-making equipment?
🔹 How do I know if my molds need to be replaced?
🔹 Are moisture sensors really worth it for dry-mix block plants?
🔹 What’s the ideal compressive strength for structural blocks?
In the precast industry, not all concrete blocks are created equal. Top producers know that a single defective block doesn’t just waste material — it can cost you clients, contracts, and credibility.
“A substandard block may seem like a minor flaw… until it causes a return order or the loss of a million-dollar tender.”
At CBM Experts, we’ve helped precast plants in over 60 countries optimize their production. We’ve seen what works, what fails, and what separates a high-performing factory from a struggling one.
Here’s the bottom line:
Block quality isn’t inspected at the end. It’s engineered from the beginning.
From the mix design and moisture control to mold precision and machine calibration, every detail matters. This article walks you through the 5 critical factors that determine whether your vibrocompacted concrete blocks are flawless — or flawed.
1. 🧪 Quality Mix: The Foundation of Every Reliable Concrete Block
When it comes to manufacturing concrete blocks with machines like the Besser Ultrapac or Quadra, the first step — and arguably the most critical — is the mix.
It’s not enough to have quality materials; the formula and process must be flawless to ensure strong, uniform blocks that comply with international standards like EN 771-3 or ASTM C90.
🔍 Why is it so critical?
The mix used in vibrocompacted block plants is semi-dry, with a very low water-to-cement ratio (typically between 0.35 and 0.40). This means that even small variations in moisture, particle size distribution, or dosing can have major consequences:
Loss of compressive strength.
Compaction issues and deformed block shapes.
Increased rejection rates due to porous or defective blocks.
In fast-paced lines running at 6–10 seconds per cycle, a single mix issue can lead to thousands of defective blocks before detection.
⚙️ Key Elements of a Quality Mix
1.1. Precise Material Dosing
Cement, fine and coarse aggregates must be measured by weight, not by volume.
Moisture variations in aggregates must be monitored to adjust water content in real time.
Use CBM’s automatic dosing systems to eliminate human error margins.
1.2. Tight Water/Cement Ratio Control
A high w/c ratio leads to porosity, lower strength, and deformation.
A low w/c ratio without plasticizers results in poorly shaped or brittle blocks.
✅ Use real-time moisture sensors (see Point 2) and superplasticizers to maintain flowability without compromising strength.
1.3. Perfect Mix Homogeneity
The mix should be short, dry but cohesive — not runny.
Overmixing can degrade consistency, while undermixing causes segregation.
The best plants establish batch-specific standards and perform consistency tests with every shift change or variation in humidity.
✅ Best Practices
Practice
Pre-moistening aggregates
Monitoring ambient temp & humidity
Standardizing mixing time per batch
Mix design engineered by experts
Direct Benefit
More predictable water absorption
Better water correction and consistency
Repeatable texture and compactability
Fewer trial-and-error cycles, higher reliability
📈 Measurable Results
✔ Up to 40% reduction in defective units
✔ More than 20% increase in compressive strength
✔ Lower cement consumption (thanks to dosing precision)
✔ Improved finish and geometry with no need for reprocessing
2. 💧 Moisture Sensors: The Technology That Guarantees Batch-to-Batch Consistency
To produce high-quality concrete blocks in vibrocompacted block plants using Besser Ultrapac or Quadra machines, the moisture level in the aggregates is a critical factor. An error of just 1% in moisture can alter 10 kg of aggregate per ton of dry material, directly affecting the strength, density, and finish of your blocks.
🔍 Why Moisture Sensors Matter
Moisture sensors (e.g., microwave or optical) measure moisture levels in real time within hoppers or mixers and automatically adjust the water dosing. Their advantages include:
✅ Batch-to-batch consistency: eliminates variability caused by ambient humidity or rainfall.
✅ Cement savings: by optimizing the w/c ratio, the plant saves both material and money.
✅ Fast return on investment: ROI within 3 to 6 months, whether producing concrete or vibrocompacted blocks.
⚙️ Recommended Sensor Types & Applications
Sensor Type
Microwave Sensors (Hydronix)
Optical Moisture Probes (Polarmoist)
In-Mixer (Hydro-Probe Orbiter)
Installed At
Aggregate hoppers
Mixer input zones
Inside the mixer itself
Key Benefits
Highly accurate, non-invasive, robust
No contact, fast calibration
Measures actual mix moisture dynamically
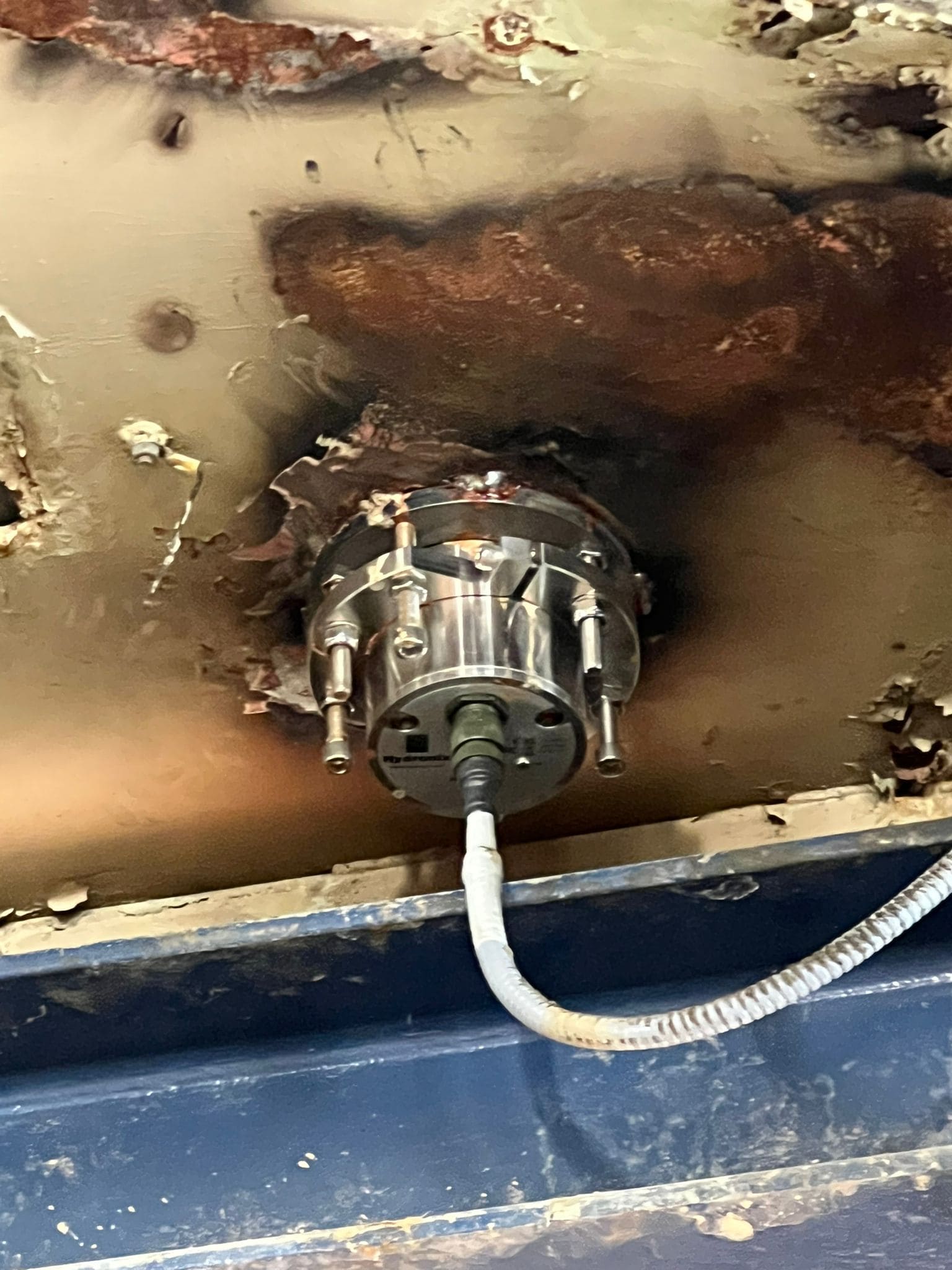
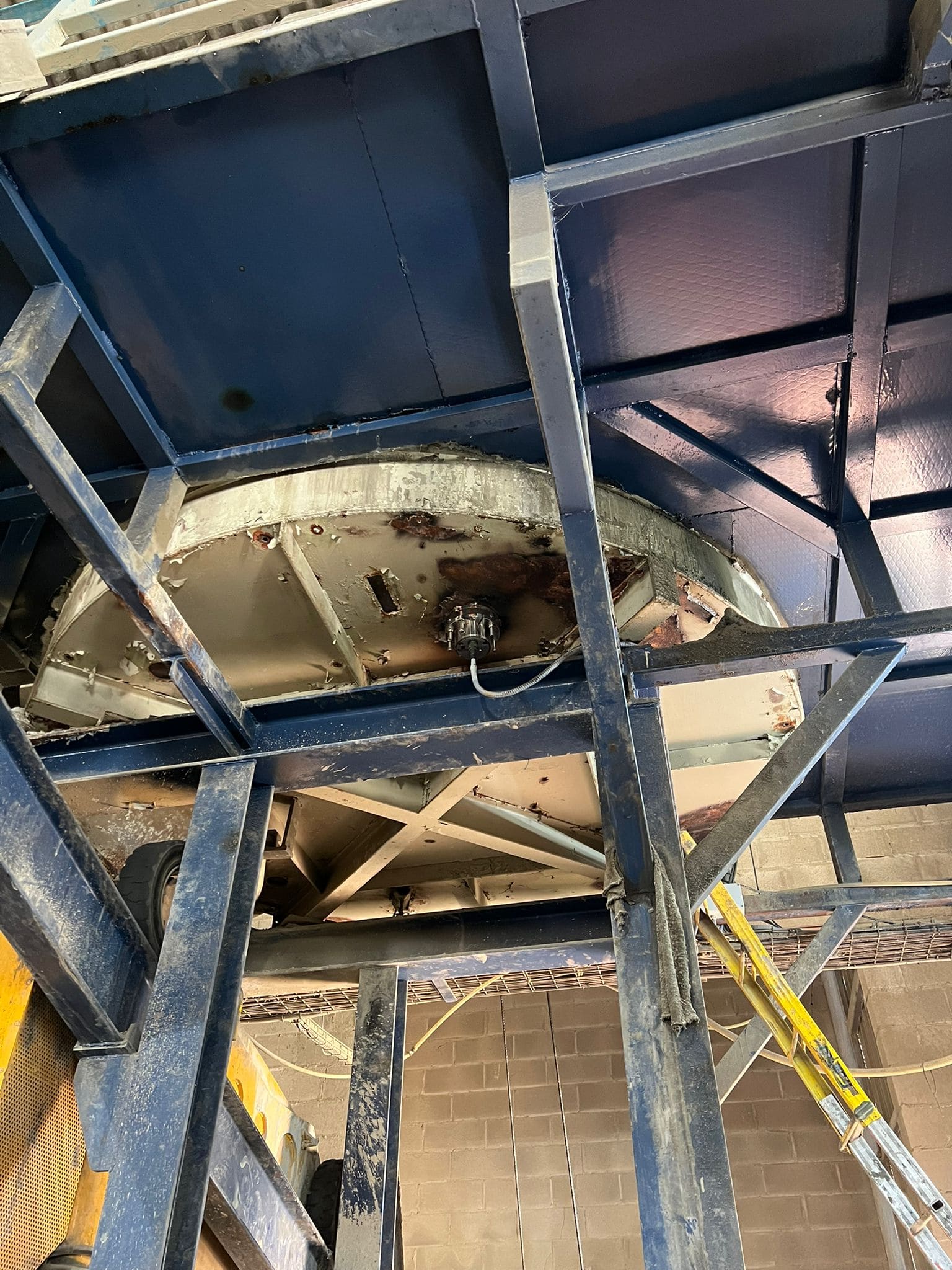
Popular systems include Hydronix, Polarmoist, and Hydro-Probe Orbiter, all compatible with PLC/SCADA for full automation integration.
🔄 Integration with Automation CBM
They connect to the plant’s PLC or SCADA system.
They automatically adjust the dosing of aggregates and water.
They enable real-time error detection and immediate correction.
“Moisture sensors transform concrete production from reactive to predictive.”
📈 Results You Can Expect
Perfect batch-to-batch mix consistency.
Increased strength without changing the formulation.
Waste reduction from defective batches.
Full process control — from raw materials to the final block.
3. 🔩 High-Quality Molds: The Unsung Heroes of Precision and Efficiency
If the concrete mix is the soul of a block, the mold is its skeleton. In high-volume production lines using Besser Ultrapac or Quadra machines, mold quality directly determines the shape, strength, and finish of every unit — and plays a key role in your profitability.
🔍 Why Mold Quality Matters
They withstand high-cycle repeated pressure — up to and beyond 1 million cycles — without losing precision.
Dimensional uniformity depends on their stability: deformations result in misaligned blocks that fail to meet ASTM or EN tolerances.
Premature wear leads to more downtime, higher spare part costs, and extra mortar use for corrections — directly impacting profitability.
⚙️ Mold Construction Standards for Top Performance
The best molds are made from:
Manufactured from S355 structural steel, often with heat treatment, powder coating, or galvanization.
Robotic inspection and welding (CNC/Trumpf systems) ensure micron-level tolerances and high repeatability.
Modular systems allow for interchangeable sidewalls using inserts, extending mold life without needing a full replacement.
🛠 Key Features to Look For
Feature
Resistance to heavy use
Dimensional consistency
Better finishes
Total cost savings
Modular flexibility
Operational Advantage
Molds last ≥10 years even with daily use
Perfectly shaped blocks with higher compatibility
Smooth surfaces, free of burrs and porosity
Fewer downtimes, less spare part use, mortar, and reprocessing
Multiple geometries without needing to purchase new molds
🧠 Best Practices for Mold Management
Select S355 steel with anti-corrosion coatings.
Use CNC welding for precision and surface finish.
Perform regular inspections and cleaning (high-pressure or shot blasting).
Replace worn inserts or sidewalls without changing the entire mold.
Implement rotating mold inventory to optimize production time.
📈 Results of Using High-Quality Molds
Up to 30% more productivity by eliminating dimensional errors
Reduced operating and maintenance costs
Improved perception from end clients (finish, precision, and reliability)
Greater competitiveness in demanding markets (structural, regulatory, civil works)
4. 🛠️ Calibrated Equipment: Precision That Pays Off in Every Production Cycle
Even with a perfect mix and high-quality molds, poorly calibrated equipment can ruin your blocks. In Besser Ultrapac, Vibrapac, or Quadra systems, small misalignments in pressure, timing, or vibration can lead to massive inconsistencies and costly rejects.
🧠 Why Calibration Is Non-Negotiable
Vibration, pressure, and compaction times determine the exact density and shape of the block.
Without precise maintenance, compaction becomes inconsistent, resulting in deformed or weaker blocks.
In high-output production lines, repeated underperformance can translate into tens of thousands of euros lost per year.
⚙️ What Needs Calibration and How Often
4.1. Vibrators and compactors
They must be synchronized to ensure uniform vibration and homogeneous compaction.
Besser and Quadra machines require frequent (monthly) checks of vibrator frequency, amplitude, and alignment.
4.2. Hydraulic or pneumatic presses
Ensure that the applied pressure remains constant in every cycle.
Compare actual pressure to nominal pressure — a drop may indicate a system on the verge of failure.
4.3. Timer and cycle control systems
The locking, vibration, and extraction cycle must be perfectly synchronized according to the machine’s manual.
Adjusting timing ensures that each block receives the ideal treatment — neither overcompacted nor underprocessed.
4.4. Sensors and actuators
Pressure and position sensors must be properly calibrated to ensure the machinery executes the cycle accurately.
A sensor failure can cause the machine to proceed even if the mold is not closed or ready.
🔧 Best Practices for Calibration & Maintenance
Establish regular calibration protocols (weekly checks of key parameters).
Use calibrated tools (pressure gauges, tachometers, test sensors).
Keep records of previous adjustments and calibrations to identify trends.
Provide in-house training for plant operators.
Implement a preventive maintenance plan aligned with quality standards.
📈 Impact on your plant
Better consistency in block shape and density, batch after batch.
Reduction in rejected or reprocessed units by up to 25%.
Fewer unplanned downtimes, more effective production.
Increased customer satisfaction and real savings in operating costs.5. 🏅 Final Block Quality: The True Measure of an Optimized Production Process
5. 🏅 High-Quality Concrete Blocks: The Result That Impacts Your Business
After optimizing the mix, moisture control, precision molds, and calibrated equipment, what truly matters is that the vibrocompacted block comes out perfect: strong, aesthetic, durable, and rejection-free. This is where the savings, efficiency, and reputation of your Besser or Quadra plant become tangible.
🧠 What Defines a High-Quality Concrete Block?
High compressive strength
Compliant with EN 771-3, ASTM C90, or UNE standards depending on the market, with safety margins above the required minimum.
Exact dimensions and batch-to-batch consistency
Blocks with millimetric precision, fully compatible on-site without the need for mortar adjustments or forced fittings.
Smooth surfaces and no physical defects
No visible pores, burrs, or stains that would compromise the final finish.
Reliable thermal and acoustic properties
Delivering declared values that ensure insulation and comfort, increasing the final product’s value.These are not just quality indicators — they’re sales tools, especially when targeting premium construction, government projects, or export markets.
💡 Why These Blocks Make the Difference
Fewer rejections and returns: every avoided defect means direct savings and less strain on staff.
Stronger reputation in tenders: flawless products are recognized and recommended in major projects.
Higher customer retention: perfect installations build trust and lead to recurring contracts.
Premium pricing: higher perceived value allows for better margins without losing competitiveness.
🔁 How to Ensure This Level of Quality
Periodic compressive strength and absorption tests by batch.
Systematic visual inspection using either AI vision systems or trained operators.
Dimensional control using calipers or 3D scanners to ensure minimal tolerances.
Batch-by-batch data logging and analysis to detect trends and take preventive action.
Ongoing staff training to identify defects and review process parameters.
Conclusion
“A high-quality concrete block is not a luxury — it’s the result of an optimized, efficient, and profitable industrial process.”
At CBM Experts, we support you at every stage to ensure your plant produces uniform, high-strength blocks that stand out in the market. We conduct technical audits that reduce rejection rates by up to 70%, increase compressive strength by 20%, and lower operational costs.
📩 Would you like us to perform a process audit to assess the real quality level of your blocks?
Request your technical report + improvement plan today.
❓ Frequently Asked Questions About Concrete Block Quality in Vibrocompacted Plants
🔹 What’s more important: the concrete mix or the block machine?
Both matter — but the mix is the root of most quality problems. A poor mix will result in inconsistent blocks, regardless of how advanced your machinery is. A high-end Besser or Quadra line can only perform as well as the material it compacts.
🔹 How often should I calibrate my block-making equipment?
Key systems like vibration units, hydraulic presses, and cycle timers should be checked weekly and calibrated every 1–3 months, depending on production volume. Calibration keeps your output consistent and avoids creeping inefficiencies that lead to rejects.
🔹 How do I know if my molds need to be replaced?
Watch for:
Block edges losing sharpness
Irregular dimensions in finished units
Increased cleaning frequency or cement buildup
Frequent sticking or incomplete demolding
CBM Experts offers mold audits and insert replacement strategies that extend lifespan and reduce costs.
🔹 Are moisture sensors really worth it for dry-mix block plants?
Absolutely. In vibrocompacted systems, aggregate moisture control is critical. Moisture sensors help optimize the water/cement ratio and reduce cement overuse. Most plants see ROI within 3 to 6 months.
🔹 What’s the ideal compressive strength for structural blocks?
Depending on standards (e.g. ASTM C90, EN 771), typical structural blocks must exceed 13–15 MPa. However, high-performance blocks can reach >20 MPa, which opens doors to premium markets and demanding tenders.
🔹 Can I automate quality control?
Yes. Many CBM clients now use:
Vision inspection systems
Digital production logs
Integrated batch traceability
This helps switch from reactive QC to real-time quality assurance, minimizing human error and cost.
🔹 How can I reduce the rejection rate in my plant?
The best results come from:
Calibrated machinery
Moisture-controlled mixing
Consistent mold maintenance
Real-time performance monitoring
Operator training + QC protocols
CBM Experts offers a holistic process audit that has helped plants reduce rejects by 40–70%.